There are various specifications to choose from for intermittent tooth profile and radial discharge rotor stator mixer styles, from laboratory sample preparation to industrial scale production.In laboratory applications, the mixing head (components of the rotor and stator) can be as small as 0.01m (Turrax, Silverson), and the amount of liquid processed can range from a few milliliters to several liters. In the industrial application model shown in Figure 5.3, the maximum diameter of the mixing head is 0.5m, which can batch process several cubic meters of fluid.
Therefore, the geometric shape of the rotor and stator produced on a large scale by Silverson is the same as that of the rotor and stator used on a laboratory scale. Similarly, the shape of Turrax's rotor stator component is actually the same across different specifications.
In practical applications, the selection of rotor stator mixers for specific emulsification processes depends on the desired product form, usually based on the average droplet size or droplet size distribution (DSD) and the size of the single batch of processed products. In open literature, there is little mention that the average droplet size of the rotor stator mixer can be calculated, and there is no method to estimate DSD. Therefore, selecting the appropriate mixer and processing conditions for a specific formula is often achieved through trial and error. Many leading manufacturers either offer a trial period for mixer use or conduct laboratory scale emulsification on a given formula, optimizing the different types/geometries of their manufactured mixers through testing. Obviously, the latter option may not be acceptable for many companies because the process they use to manufacture lotion based products is commercially sensitive. Once the type of mixer and its operating parameters are determined in the laboratory scale, it is necessary to scale up the process to the production scale.
Most emulsification laboratory tests are conducted in small batch containers because it is easier and cheaper than continuous operations. Therefore, before expanding the scale of the rotor stator mixer, it is necessary to decide whether industrial emulsification should be carried out intermittently or continuously. For processes that require a longer processing time (usually associated with slow chemical reactions) for product formulations, it is recommended to use an intermittent mixer. They require a simple control system, but spatial uniformity in large containers may be an issue, which can lead to longer processing times. In the process of controlling product quality through mechanical/fluid dynamics interactions between continuous and dispersed phases, or through rapid chemical reactions, a significant amount of energy is required to ensure sufficient mixing. It is recommended to use an online rotor stator mixer. Online mixers are also recommended for effectively handling large tonnage fluids.
In the case of intermittent processing, the use of a top inlet inlet mixer (Figure 5.4a) in the rotor stator device is the simplest mechanical arrangement, but in some processes, the bottom inlet mixer (Figure 5.4b) can ensure better batch mixing, but in this case, the sealing is more complex. Usually, due to the limitation of the mixing capacity of the mixer without dead corners, the efficiency of the intermittent rotor stator mixer will decrease with the increase of container size and the viscosity of the processed liquid. If the apparent viscosity of the liquid/lotion is low, Turrax's open structure mixer can often carry out full mixing without dead corners even in relatively large containers. However, for processing very viscous lotion, additional impeller (usually anchor shaped) is required to guide and circulate lotion through rotor stator mixer. On the other hand, the pumping capacity of intermittent Silverson rotor stator mixers is very limited, and even on a laboratory scale, they can be installed outside the center of the container (eccentric installation) to improve the overall mixing effect. On a large scale, at least one additional impeller is always required (Figure 5.3b), and for very large container units, multiple impellers need to be installed coaxially to facilitate flow guidance.
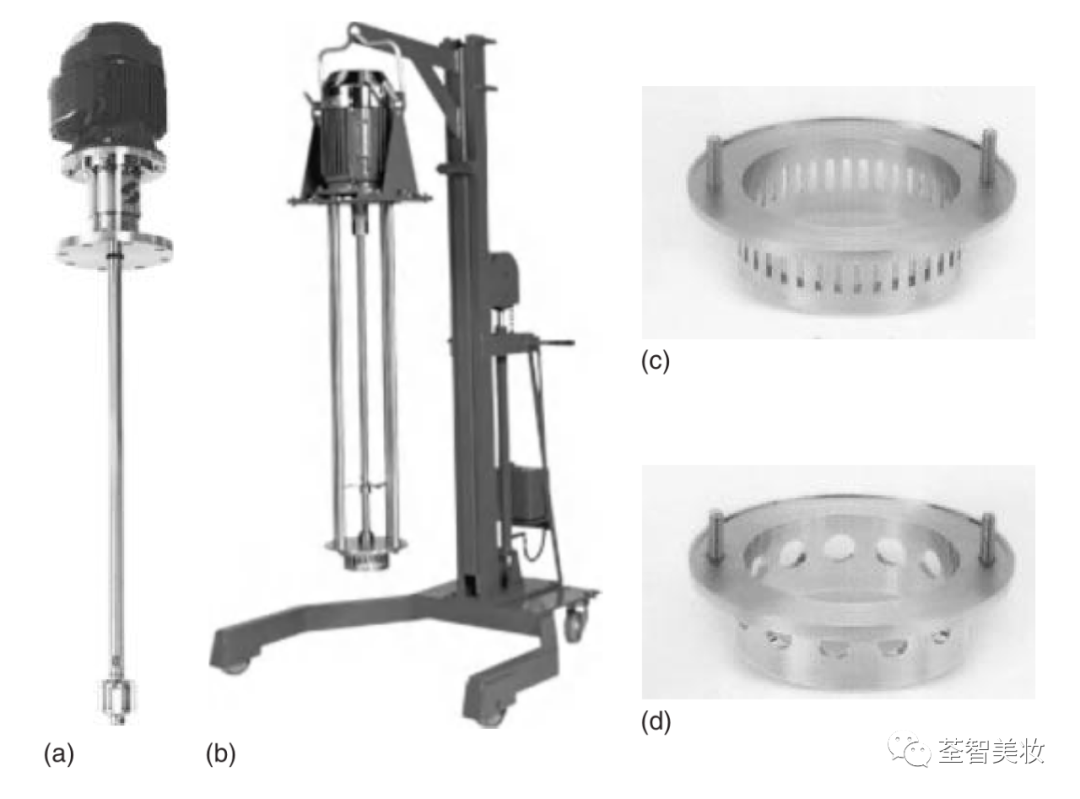
Figure 5.3 Industrial scale rotor stator mixer: (a) Toothed mixer - IKA Medium Ultra Turrex, maximum batch size 6m3; (b) Large Silverson intermittent radial discharge mixer with a maximum batch volume of 35m3; (c) The slotted screen (maximum diameter 0.5m) used in mixer (b), and the crushing screen (d) used in mixer (b)
There are still mechanical issues when installing large heavy-duty mixers in large containers. Firstly, the weight of the motor/shaft assembly needs sufficient support. Secondly, long shafts rotating at speeds of thousands of revolutions per minute may require additional support/bearings to avoid vibration and oscillation. These issues can be avoided by installing the agitator at the bottom of the container with a shorter and more stable shaft (Figure 5.4b), but in this case, appropriate seals must be used. Moreover, the distance between the mixer and the bottom of the container is very close, which further limits the pumping capacity of the mixer. Therefore, in this configuration, additional impellers are required for dead angle mixing.
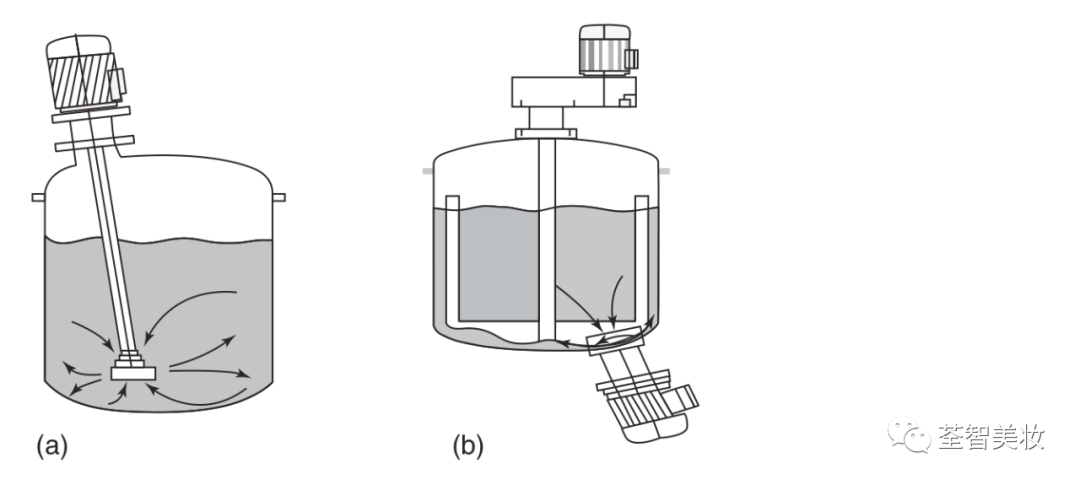
Figure 5.4 (a, b) Possible arrangement of rotor stator mixer during intermittent process treatment
The use of intermittent rotor stator mixers to handle large amounts of fluid can be avoided by replacing the intermittent mixer with the online (continuous) mixer briefly discussed earlier. Different suppliers (such as Silverson, IKA, etc.) offer many design models to choose from, and the geometric differences between the rotor and stator are mainly related to the design schemes of the stator and rotor being suitable for different application purposes. The main difference between intermittent rotor stator mixers and online rotor stator mixers is that the latter has strong pumping capacity, so they are directly installed in pipelines. One of the main advantages of online rotor stator mixers compared to intermittent mixers is that for the same power load, online mixers require a much smaller mixer, making them more suitable for handling large amounts of fluid. When the scale of the container increases and reaches a certain point, using an online rotor stator mixer will be more effective than increasing the diameter of the intermittent mixer. Because power consumption increases sharply with the increase of rotor diameter (up to the fifth power), a very large motor is required for large diameter hybrid rotors. The transition point depends on fluid rheology, but for fluids with viscosity similar to water, it is recommended to switch from an intermittent rotor stator mixer to an online rotor stator mixer process for processing liquids with a volume of approximately 1-1.5 tons.
Most manufacturers offer both single-stage and multi-stage mixers, the latter being recommended for higher mixing processes, such as emulsification of high viscosity liquids or processing/particle size reduction in solid/liquid systems. Examples of single-stage and two-stage rotor stator mixers are shown in Figure 5.5.
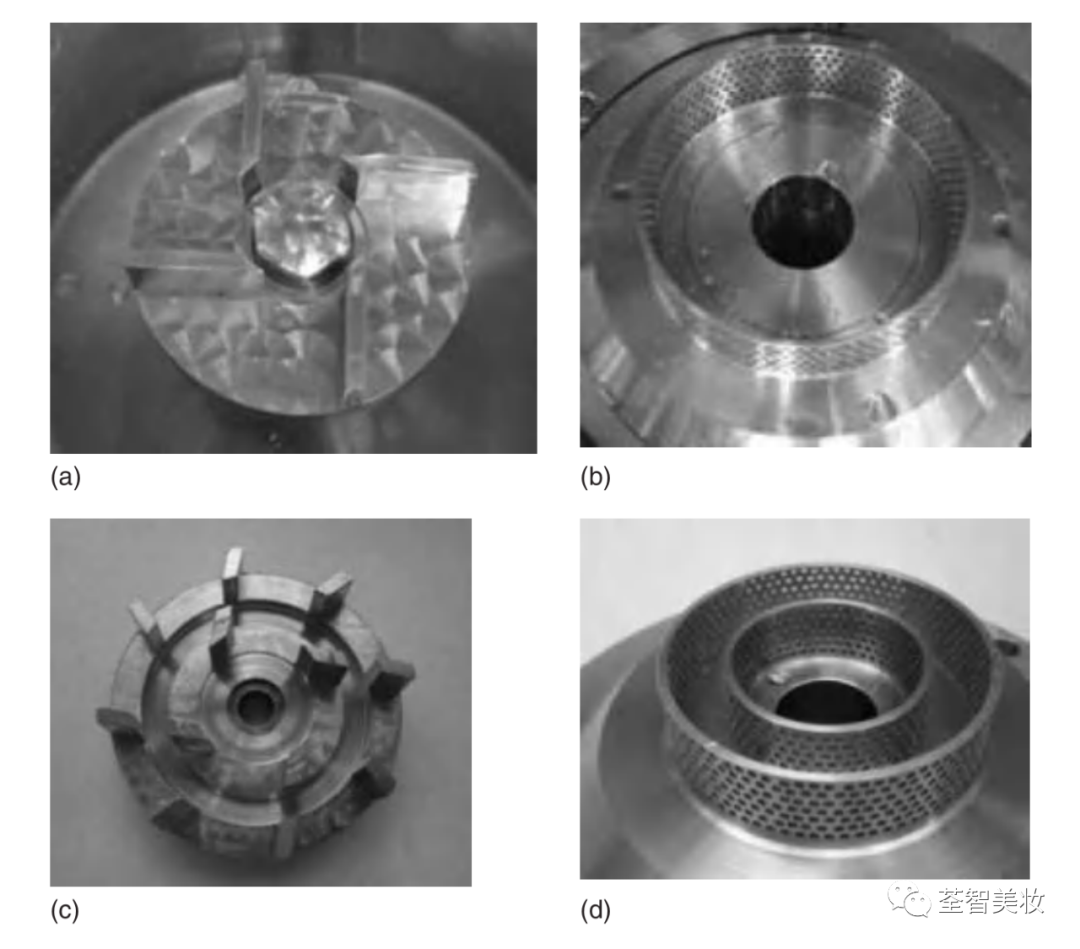
Figure 5.5 Geometric shape of Silverson's online rotor stator mixing head (64mm diameter): (a) single-stage rotor and (b) single-stage stator; (c) Double stage rotor and (d) double stage stator
Jinzong Enterprise has been focusing on the research and development and manufacturing of emulsification homogenization equipment for more than 20 years. We can customize various homogenization emulsifiers to meet the needs of large-scale production and laboratories. We welcome customers to inquire, negotiate, and visit for guidance!
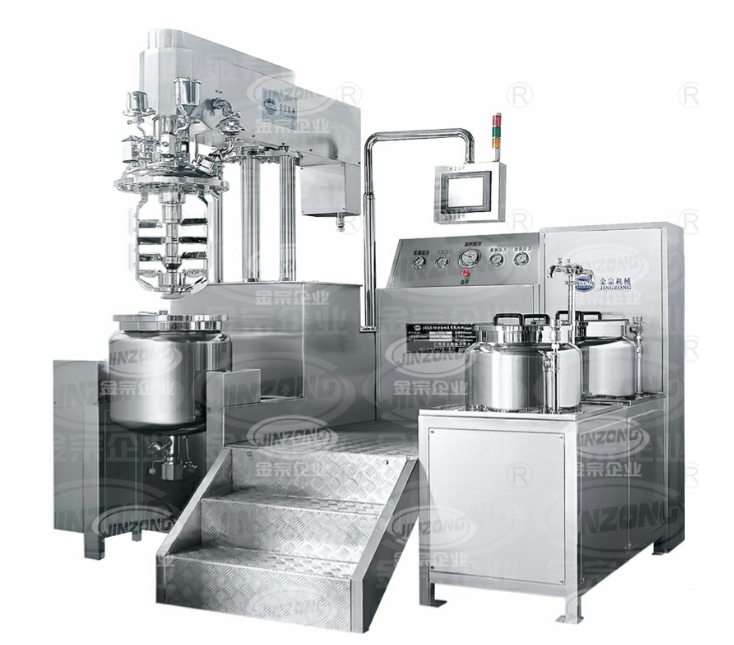