In the cosmetics,pharmaceutical,food and other industries,vacuum paste machine as a core equipmemt for efficient and accurate preparation of various paste, emulsion products, such as skin care products, ointment, toothpaste, food sauces and so on.Purchasing a suitable vacuum paste machine is crucial to ensure product quality,improve production efficiency and maitain enterprise competitiveness.This article will detail the purchasing points of vacuum paste machine,aiming at providing a pratical purchasing guide for enterprise decision makers.
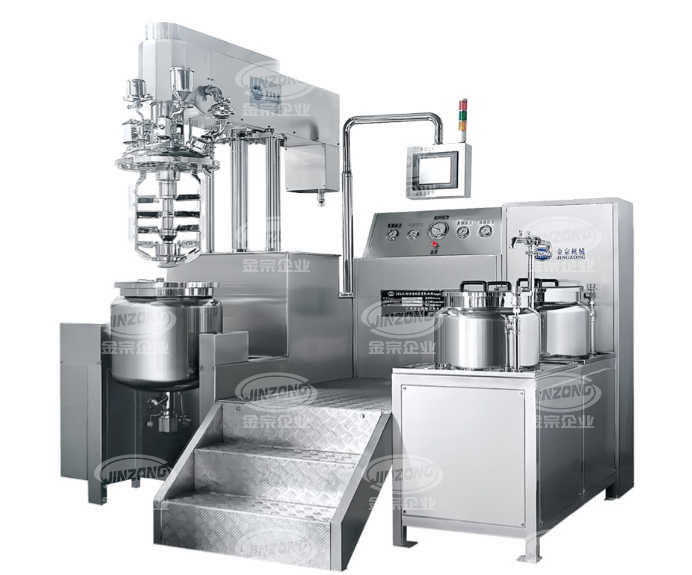
一、Clear Production Needs and Product Characteristics
1.Production Capacity and Batch Scale.First,according to production plan and expected yield of enterprise,determine the processing capacity of the required equipment.Select the appropriate valume of vacuum paste machine,such as 50L,100L,200L,500L and other different specifications to meet the needs of mass production, while avoiding excessive investment caused by waste of resources.
2.Product Types and Formulations.Understand the specific types of products to be prepared (e.g. skin creams, toothpastes, food sauces, etc.), ingredient complexity, viscosity range, and special process requirements (e.g. heating, cooling, long stirring, etc.). These factors will directly affect the functional configuration of the equipment, such as whether it needs to have heating and insulation function, cooling system, high shear homogenization function, etc.
二、Equipment Performance and Technical Indicator
1.Vocuum Performance.Vacuum degree is an important indicator for measuring the degassing effect of a paste making machine. High vacuum degree helps to effectively remove air from materials, prevent product oxidation, extend shelf life, and ensure the smoothness and stability of the paste. When selecting, attention should be paid to the maximum vacuum degree, vacuum holding capacity, and stability of the vacuum system of the equipment.
2. Homogenization and Stirring Ability. An efficient homogenization system can ensure that the material particles are fully refined and achieve the ideal dispersion state. Inspect the homogenization speed, shear rate, homogenization head structure (such as fixed rotor type, high shear type, etc.) and adjustability of the equipment to ensure that it can meet the homogenization requirements of different product formulations. At the same time, the mixing system should have good mixing efficiency and mild processing methods to avoid excessive shearing or damage to the thermosensitive components of the material.
3. Temperature control accuracy. For temperature sensitive products, the equipment should have precise and stable temperature control functions, including heating, cooling, and insulation capabilities. Check the heating power, cooling medium flow control, and temperature sensor accuracy of the equipment to ensure precise temperature control throughout the entire paste making process.
三、 Equipment material and manufacturing quality
1.Stainless steel material. Choosing a paste making machine made of high-quality stainless steel (such as 304 or 316L) to ensure that the equipment is corrosion-resistant, easy to clean, and meets the hygiene standards for food and drug production. Check the polishing degree, welding quality, and dead angle free design of the internal and external surfaces of the equipment to reduce the risk of microbial contamination.
2. Sealing performance. Excellent sealing components and sealing design are key to ensuring stable vacuum and preventing material leakage. Evaluate the sealing materials and design rationality of equipment's shaft seals, flange connections, valves, and other parts to ensure good sealing performance is maintained during long-term operation.
四、 Degree of automation and intelligence
1.Control system. Advanced control systems such as PLC or touch screen interface can achieve precise setting of process parameters, real-time monitoring, data recording, and fault alarm functions, improving production efficiency and process reproducibility. Choose a control system with a user-friendly interface, easy operation, and programming.
2. Automation function. Consider whether the equipment has functions such as automatic feeding, discharging, cleaning, and CIP (on-site cleaning) to reduce manual intervention, labor intensity, and human error, while improving equipment utilization and the overall automation level of the production line.
五、 Supplier Qualification and After sales Service
1. Brand reputation and industry experience. Choose equipment manufacturers with good reputation, rich experience, and successful cases in the industry, such as Guangdong Jinzong Machinery Co., Ltd. and other well-known manufacturers. Their products are often market validated, technologically mature, and of reliable quality.
2. Technical support and after-sales service. Assess whether the supplier can provide comprehensive after-sales services such as professional technical consultation, installation and debugging, operation training, maintenance, and spare parts supply. High quality after-sales service not only ensures the normal operation of equipment, but also provides timely and effective solutions when encountering problems.
六、 Economy and investment return
1. Equipment procurement cost. On the premise of meeting production needs, compare quotes from different manufacturers, consider equipment procurement costs, including the price of the equipment itself, supporting equipment (such as vacuum pumps, condensers, etc.), installation costs, and possible taxes and fees.
2. Operating costs and energy efficiency. Evaluate the energy consumption, maintenance costs, service life, and potential upgrades of the equipment. Choosing equipment with high energy efficiency, simple maintenance, and strong durability is beneficial for reducing long-term operating costs.
3. Investment return analysis. Based on factors such as equipment performance, production efficiency improvement, product quality improvement, and potential market opportunities, calculate the return on investment to ensure that equipment investment meets the financial goals of the enterprise.
In summary, choosing a vacuum cream making machine is a decision-making process that involves multiple considerations. Enterprises should comprehensively evaluate key factors such as equipment performance, quality, automation level, and supplier services based on their own production needs, product characteristics, budget constraints, and long-term development plans, in order to select the vacuum cream machine that is most suitable for their business development. In this process, in-depth communication, on-site investigation, machine testing and verification, as well as reference to industry expert opinions, are all indispensable steps to ensure the scientific and accurate nature of the final procurement decision.