Detailed explanation of operation, maintenance, and common trouble shooting of reaction vessel
A reactor is an important equipment widely used in industries such as chemical, pharmaceutical, and food for physical or chemical reactions. Jinzong Enterprise, with over 20 years of experience in reactor production and research and development, will provide a detailed introduction to the operation, maintenance, and common troubleshooting of reactors.
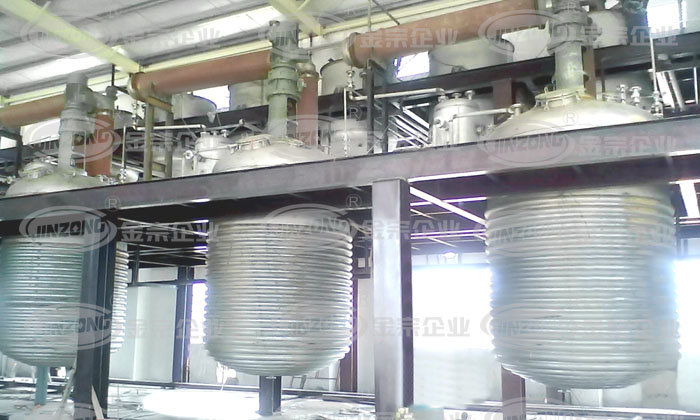
1、 Operation steps of reactor
Preparation before starting up: First, confirm that there is no looseness or leakage in the connection parts of the reactor, the power circuit is normal, and auxiliary equipment such as the cooling system and stirring device are running normally. Then, according to the reaction requirements, perform appropriate cleaning and disinfection inside the kettle, and ensure that there are no impurities inside the kettle.
Material addition: According to the requirements of the reaction process, first evenly add solid materials into the reactor through the feeding port, then slowly inject liquid materials, and at the same time, turn on the stirring device to ensure uniform mixing of materials.
Temperature and pressure control: Start the heating or cooling system to precisely control the temperature and pressure inside the reactor. During the reaction process, relevant data should be regularly checked and recorded to ensure that the reaction is carried out within the set safety parameter range.
End of reaction and discharge: After the reaction is completed, turn off the heating, cooling system, and stirring device. Wait until the temperature inside the reactor drops to a safe range before opening the discharge port for unloading.
2、 Maintenance of reaction vessel
Daily cleaning: After each use, the inside of the reactor should be cleaned in a timely manner to avoid residues affecting the next reaction effect or corroding the reactor body.
Regular inspection: Regularly inspect the functions of various equipment in the reactor, such as agitators, temperature sensors, pressure gauges, etc. If any abnormalities are found, repair or replace them in a timely manner.
Anti corrosion and rust prevention: For reaction vessels made of metal materials, regular application of anti-corrosion paint or other anti-corrosion measures should be taken to prevent rusting of the vessel body.
Seal replacement: Seals are crucial components to ensure the sealing performance of the reactor, and should be regularly inspected and replaced as needed to prevent leakage.
3、 Common troubleshooting of reaction vessel
Temperature out of control: If the temperature cannot be accurately controlled, first check whether the temperature control system and thermocouple are normal. If there is any damage, repair or replace it immediately; Secondly, confirm whether the amount of material in the kettle and the heat transfer medium are suitable, and adjust them if necessary.
Abnormal pressure: Excessive or insufficient pressure may be caused by a malfunction of the pressure relief valve or blockage of the intake/exhaust system, which requires prompt investigation and resolution.
Stirring failure: If the mixing device is not working or unstable, the motor, reducer, and mixing shaft should be inspected to eliminate mechanical faults. If necessary, damaged parts should be replaced.
Leakage problem: Once a leakage is found in the kettle or pipeline, the reaction should be stopped immediately, and the leaking area should be repaired or the sealing ring replaced to ensure the safe operation of the equipment.
In summary, proper and standardized operation of the reactor, regular maintenance, and quick and effective handling of various faults can not only ensure the safety and efficiency of the production process, but also extend the service life of the reactor, bringing better economic benefits to the enterprise.
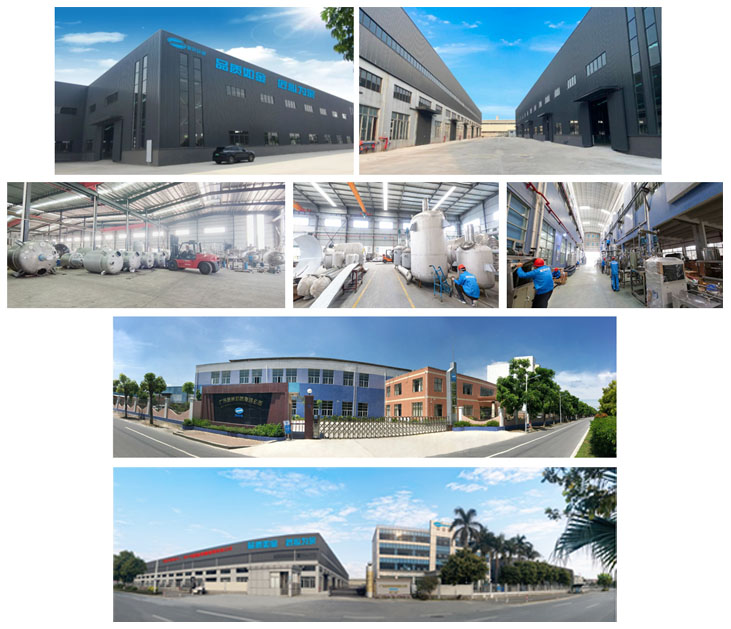
Jinzong Enterprise was founded in 1999, specializing in the design and manufacturing of mechanical equipment, research and development of intelligent control systems, and engineering design and installation. The main products include synthesis reaction production lines, vacuum emulsification production lines, mixed extraction production lines, water treatment equipment, etc., which are widely used and mainly serve and apply in the automation production of fine chemicals, coatings, pharmaceuticals and food, automotive products, cosmetics, new energy materials, and other fields.
Jinzong owns several wholly-owned companies, including Guangdong Jinzong Machinery Co., Ltd., Jinzong Technology (Guangzhou) Co., Ltd., and Jinzong Intelligent Technology (Guangzhou) Co., Ltd. There is a design and marketing service center in Guangzhou, and two production factories have been built in the Zhaoqing National High tech Zone. They have the qualifications for special equipment pressure vessel manufacturing and pressure pipeline installation (GC2), and are a national high-tech enterprise and a provincial-level specialized and refined new enterprise. They have two provincial-level branded products, dozens of product patents, software copyrights, and provincial-level high-tech products. They have passed the national intellectual property standard certification, ISO9001-2015 international quality system certification, and EU CE certification, and have been awarded the title of "Guangdong Province Contract abiding and Creditworthy Enterprise" by the Guangdong Provincial Administration for Industry and Commerce for many years. They have users in more than 50 countries and regions around the world, and have been widely recognized and supported by more than 2000 small and large enterprises at home and abroad.
To do a good job, one must first sharpen their tools. Jinzong Enterprise upholds the concept of "quality is like gold, craftsmanship is the core", and provides advanced and automated production lines to manufacturing factories. Friends from home and abroad are welcome to visit and guide us!